Effect of Lubrication on Vibration Response and Surface Finish in Milling Aluminum 6061
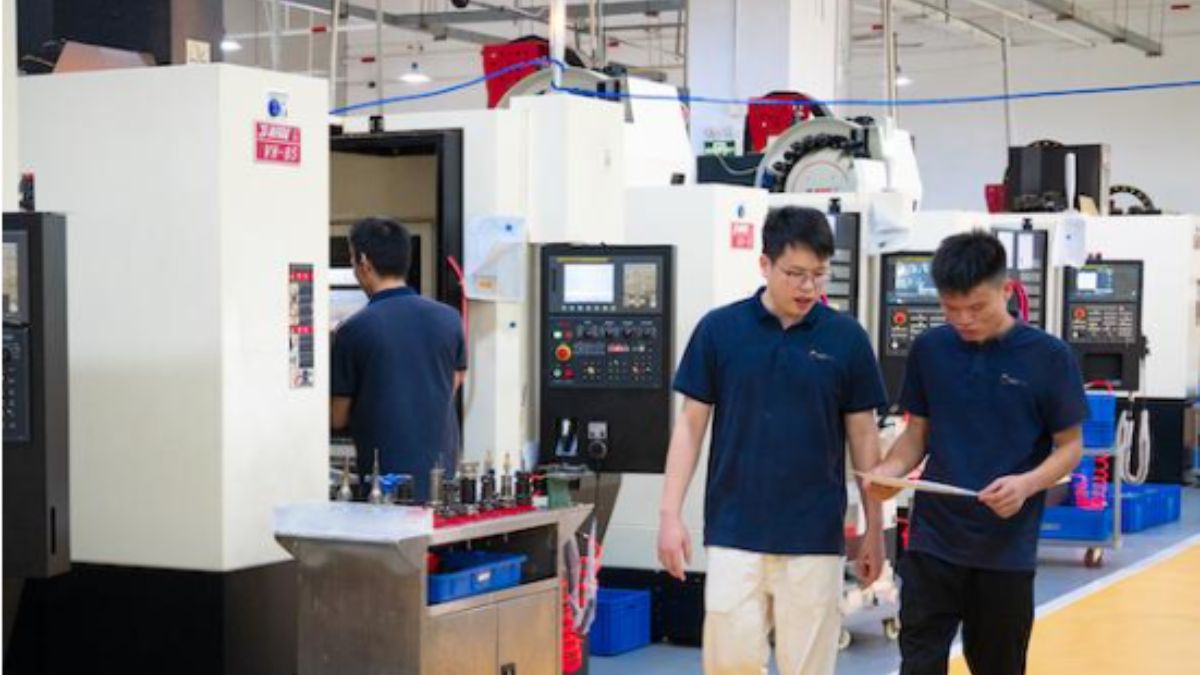
Aluminum machining excels with its lightweight materials and resistance to corrosion, which leads manufacturers to choose aluminum 6061 for many structural parts and prototype builds. Its malleable nature and strong affinity for cutting tools cause excessive friction and lead to vibrations during machine operations. Lubrication reduces friction between the tool and material, extending tool life, minimizing vibration, and enhancing surface quality, ultimately optimizing the production process.
This study explains how lubrication affects vibration control, surface texture quality, tool life, and milling performance when working with Aluminum 6061 to provide recommendations for maximum output.
Influence of Lubrication on Vibration Damping
During aluminum 6061 milling operations, the right amount of lubricant controls vibration behavior. When there is not enough lubrication between the tool and workpiece, the friction rises, which makes tool vibrations stronger and creates chattering. Chatter occurs when the stress interaction between the tool and material becomes unstable. As friction grows stronger, the tool moves excessively, causing uneven surface areas and loss of part accuracy in dimensions. The vibrations impact both the project output and put excessive pressure on the milling machine during operations.
Companies like WayKen, a leader in precision machining services place great emphasis on making custom lubrication strategies for each job. WayKen chooses lubricants that reduce aluminum metal surface contact while working with Aluminum 6061’s material characteristics. Most companies use either water-based emulsion or MQL (minimum quantity lubrication) systems to reduce vibration during machining. Quality lubrication reduces cutting forces that normally destabilize the process and delivers high-performance outcomes because it produces smoother surfaces with tighter specifications.
Impact on Surface Roughness and Tool Marks
The quality of milled Aluminum 6061 surfaces depends fully on proper lubrication. When you work without lubrication or dry machine aluminum it produces faster tool breakdown and raises the heat that hurts surface quality. The aluminum softens and spreads across the tool without lubricant to transport heat so markings from the tool remain visible and increase the surface texture. Achieving the required mirror surface quality is difficult when aluminum machining due to production requirements.
High values of surface roughness combined with tool marks don’t only damage appearance but create weakness points that may result in component failure under stress. Researchers demonstrate that proper use of synthetic cutting fluid decreases thermal pressure and stops aluminum from sticking to milling tools. The process creates better surface quality and less material irregularities which match precision standards of aluminum industries.
Lubrication’s Role in Tool Wear and Machining Stability
Lubrication directly affects the continuous degradation of tools that occurs while milling Aluminum 6061. Tool degradation happens faster when lubrication is inadequate because it permits excessive heat and friction to damage the cutting edge. The tool geometry progressively shifts when it wears down, which leads to higher vibrations and unfavorable effects on surface finish. The feedback mechanism operates with wear contributing to increased tool instability, which then accelerates the wearing of the tool, resulting in a shortened life and increased costs.
The selection of proper lubrication systems in aluminum machining leads to a reduction of these machining effects. Supplying tools with anti-wear additives through oil-based lubricants creates protective films, which decrease the tool-to-workpiece contact. Machining stability increases due to continuous cutting forces, which reduce operational vibrations, also known as chatter. A stable process serves two essential purposes: the protection of the tool, along with the production of uniform finishes across numerous parts, which is vital for batch production.
Balancing Lubrication for Optimal Performance
Utilization of optimal lubrication amounts is necessary to reach superior vibration management and surface finish quality in aluminum 6061 milling operations. An excess of lubricant allows reinserted evacuated chips to recut which produces surface defects while increasing tool stress. Hights and inadequate lubrication cause more heat accumulation that heightens both surface roughness and destructive vibrations. The operational success depends on optimizing lubrication flow according to the combined configuration of feed rate and spindle speed and cutting depth parameters.
High-speed milling operates best with MQL technology because this method streams fine lubricant droplets to the cutting area to decrease heat while avoiding excessive workpiece wetness. The management of heavy cuts demands flood cooling systems because they excel at controlling heat buildup during operations. The process requires specialists to make several sequential improvements in these operating variables while they track vibration signature patterns along with surface quality measurements to optimize the production. A systematic methodology allows lubrication systems to enhance operational efficiency through appropriate methods while avoiding supplementary performance problems and achieving optimal performance.
Lubrication interacts comprehensively with machining parameters due to their complex nature. Lubrication minimizes both the effects of machine speed on heat formation and feed rate control of chip development. The mechanical stress on the tool depends on cutting depth so manufacturers need to determine the correct amount of lubricant to apply. Manufacturers who properly align these factors will reduce vibration while minimizing tool wear to deliver exceptional surface finishes when machining aluminum.
Conclusion
Effectively milling Aluminum 6061 needs lubrication as its core component to modify vibration response and surface finish formation. The application of inadequate lubrication increases this process’s friction and generates unwanted chatter that results in both unacceptable dimensional deviation and rough surface finish yet applying unnecessary lubrication poses the risk of chip re-black and performance deterioration.
Applied correctly lubricating substances both suppress tool vibrations and minimize tool erosion and maintain optimal surface quality which resolves aluminum machining problems. Specific optimization of MQL or flood cooling processes enables production of high-quality machining results.